How to Build a Building
- Jewel Barua
- Apr 16, 2020
- 7 min read
The construction process of a building can be a long, complicated, and expensive one. Depending on your level of expertise, however, you may be able to save quite a bit of money by doing some or even all of the work yourself. You can use the same fundamentals of building construction to guide you when building large, complex structures as well as small, simple ones like sheds or treehouses. Remember to adhere to all local and national laws pertaining to constructing the type of building you choose.

Part 01: Planning a Successful Build
01. Identify your build site.
Make sure to choose a location that is on your property and meets your specific needs. A garage needs street access, but a workshop may not. Consider what purpose the building will serve, what utilities will need to be run to it, your construction limitations, and your budget when finding a spot.
Think about how you’ll get the concrete and lumber to your build site and if it needs vehicle access.
The more level the site is, the cheaper and easier it will be to prepare for building.
02. Consider neighbours, sunlight, and property lines when planning the structure.
If your building will have windows, you may want to orient them to get sun in the mornings or afternoons. Position the main doorway on the side of the building you’ll commonly approach it from. Develop a plan in your head for how you want the building to face and where entrances, exits, and walkways may need to be.
If your structure will be for a business, you may want the door and large windows facing the street.
If you are building a garage, the garage bay door needs to be oriented toward the street as well.
If you are building a workshop or out-building, you may want to front door pointed at the back door of your house, since that’s where you’ll be approaching it from.
03. Hire an architect to design your building.
Designing a building is a complex process that is best left to the professionals. Depending on the type of building you want, you may be able to purchase off-the-shelf construction plans (for garages, outbuildings, and even houses). However, for a specialized project, you should enlist the services of an architect to ensure your building is designed to be environmentally sound and within local codes.
Many architects can create plans for buildings ranging from simple to complex, with pricing that usually matches complexity.
Pre-fabricated structures like sheds and even garages come with the plans and supplies you need
04. Secure the appropriate permits.
There are a number of different permits you may potentially need to secure before you start construction, depending on where you live, the size of the building, and what the building will be used for. Contact your local town or city government office ( like RAJUK for Dhaka CDA for Chittagong, UNION or POUROSHAVA ) to inquire about building permits and how to go about getting the ones you need or contact with your architect.
Many town and city governments have websites devoted to helping you locate and apply for the correct permits ( for RAJUK http://cp.rajukdhaka.gov.bd )
Do not begin construction without securing the necessary permits, or you may be subject to legal penalties or fines.
05. Use the plans to determine what work you can do yourself.
Once you have a building plan, you can begin to break the project down into a sort of to-do list. You may want to do all of it yourself, or you may need to outsource some of the work to local contractors. Decide what you can and can’t do on your own beforehand so you can set up your budget.
Contact your Consultant (Architect & Engineers) for construction drawing
The job will require building various types of framing with steel, RCC, starting with a frame for the foundation and continuing through the walls and roof.
You will also need to pour a large amount of concrete for the structure’s foundation, which may require the use of a concrete delivery service.
Wiring, HVAC, and plumbing may be concerns depending on the size and use of your building.

Part 02: Laying the Foundation
01. Level the build site.
This process may be simple or difficult and expensive, depending on the site you’ve chosen. For small buildings, you may be able to level the site using a shovel and a tamp. However, for large buildings, you may need to use heavy machinery like a bulldozer.
Drive stakes into the ground at all four corners of the building site, then tie a string from post to post, using a level to ensure they are perfectly straight. From there, measure the distance from the string to the ground in different spots to see how high or low they are compared to the rest. Then add or remove dirt as necessary.
Once the surface is even, tamp it down so it’s firm and flat.
02. Pour the concrete foundation.
First, use the stakes you laid out to guide you as you install the right size lumber for your specific foundation. Different structures will have different depth requirements for the concrete, so adhere to the specifications on your building plan. Once the forms are complete, either pour the concrete yourself or hire a concrete delivery service to pour it for you.
You can purchase concrete by the bag and mix it yourself, but for larger applications, you may want to have a concrete delivery service pour pre-mixed concrete straight into your forms from the truck.
Follow the instructions from your construction drawing provided by the consultant.
03. Add rebar or mesh to the concrete for strength.
Adding the additional steel for support will strengthen the building’s foundation and reduce the chances of cracking or damage. Follow
You can buy either mesh or rebar at your local hardware store.
Insert the steel reinforcement about halfway through your pour so it will have concrete above and below it.
Follow the instructions from your construction drawing provided by the consultant.
04. Finish pouring the concrete and let it set for 24 hours.
After the metal reinforcement is set, fill the wood forms the rest of the way with concrete and then brush off any excess to ensure the surface is perfectly flat.
Allow the concrete to cure for at least 24 hours before doing any more work on the structure.
05. Have the site inspected if applicable.
Depending on where you’re doing the construction, you may now need to have an inspector (engineer, architect & authority) evaluate your foundation before you can set about framing the walls. If your local ordinances require an inspection, have them come once the concrete has cured.
You can find out what inspections are necessary and how to schedule them on your local authority.
Failing to schedule mandatory inspections could result in fines. The inspections are intended to ensure your structure is being built safely.
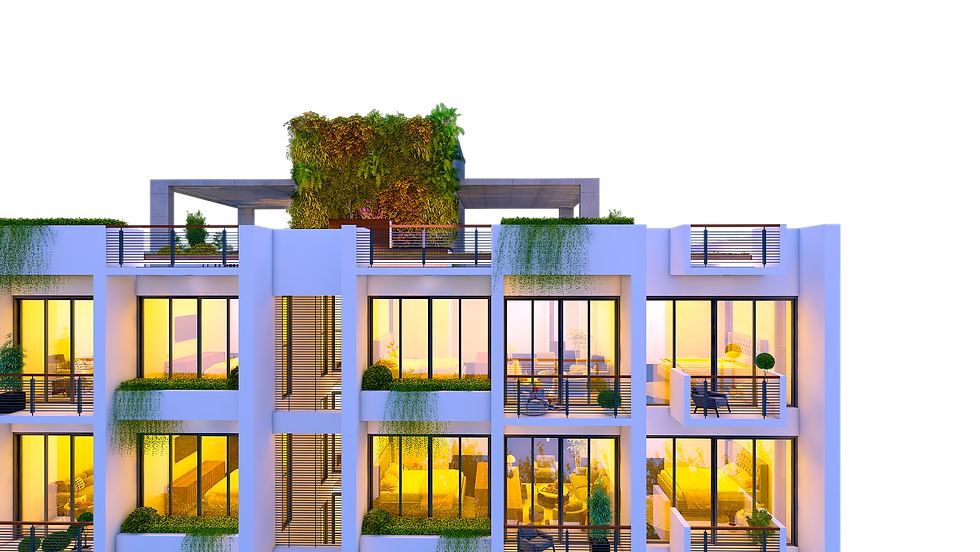
Part 03: Constructing a Shell
01. Contact your local lumber yard to help with your materials list.
Instead of purchasing the wood from your local hardware store (which may not be feasible depending on the size of your project), contact your local lumber yard and use the architectural plans to place a large order of all the wood you’ll need. Many lumber yards will even deliver the order to you.
Ordering large amounts of wood at once will reduce the overall cost.
Lumber yards can often help you determine exactly what you need based on your plans thanks to their experience with construction firms.
02. Frame the exterior wall or Structural Element.
On smaller buildings, build the wall first, then have friends help you raise the wall and secure it in place. On larger buildings, however, you’ll need to build the Structural frames directly onto the foundation.
Follow the plans for your building specifically when building and placing the wall or frames.
Pay close attention to detail while building the walls/frames. One incorrect measurement could result in an uneven wall that could create a gap between the top of the wall and the roof.
03. Add temporary wall bracing for support.
Until all of the walls are completed and the roof is installed overhead, you can keep the walls standing properly by screwing temporary beams of wood into the walls that connect them to one another. These beams should be removed once you install the roof trusses.
Use screws rather than nails so it’s easy to unscrew the braces when the structure is stable.
This step is often only necessary until the full-frame is complete.
04. Construction the slabs.
You may purchase completed trusses from the lumber supply company, or you may prefer making them yourself. Roof trusses can be complex and time-consuming, so purchasing completed ones is often preferred. Attach them to the tops of the frame walls, lining up the trusses with the studs.
Larger building may utilize a different roof framing, but trusses are the most common for small structures.
05. Call in the inspectors.
At this stage, you may need to have the building inspected again to ensure your structure is up to code. Refer to local ordinances to know for sure what inspections your specific type of building is subject to.
The inspectors will be looking at building materials, stud spacing and signs of damage.

Part 04: Finishing the Structure
01. Run the wiring, HVAC, and plumbing through the walls.
Traditionally speaking, plumbing should be done first, followed by HVAC and electrical wiring, but in practice, elements of each project will overlap. These jobs may be best left to plumbers and electricians, as they require specific skills and expertise.
Have contractors tasked with each job work together to coordinate the installations.
Ensure there is no electricity flowing to the structure when working on its wiring.
02. Install permanent fixtures that may affect wall placement, like bathtubs.
Before the interior walls are finished, move large fixtures into place and position them where they will be once the building is complete.
It’s easier to move large things into place before all the walls are finished.
You’ll need to know the positioning of things like bathtubs and toilets when installing interior walls.
03. Put in the insulation if applicable.
Sheds and some garages are often not insulated, but if your building will be, there are a number of options to choose from. Blanket insulation is the most common for new construction and can be unrolled between the studs of the walls and stapled into place.
You could also wait until the interior walls are in place and then add loose-fill or blown-in insulation into the gap between the exterior and interior walls.
Always wear eye protection, a particulate mask, and gloves when working with fibreglass insulation.
04. Finish the interior walls and ceiling.
Measure and cut each piece of drywall, then have a friend help to put it in place. Screw the drywall into the wall studs to secure it. Then repeat that process to hang the ceiling drywall as well. Once all the drywall is in place, tape and mud it to give the drywall a smooth, paintable finish.
Once the drywall is done, you can paint the interior walls.
You may also choose to cover the drywall with wallpaper.
#Architecture #building #construction #permit #RAJUK #CDA #Drawing #Design #Engineer #Architect #Designer #Steel #Cement #RCC #s16a #studio16architects #s16architects #dhakaarchitects #dhakaengineers #architects #engineers #architectural #firm #consultant #bangladesh #realestate #buildingpermit #rajukrules #dhaka #bd #bdarchitects #bdengineers #Interior #wall #column #footing #site #survey #deigitalsurvey #soiltest #soilinvestigation #soil #house #home #apartment #duplex #triplex #livingspace #space #officebuilding #officespacedesign
Comments